Stracture and Control Laboratory, Structural Mechanics Research Group
Department of Aerospace Engineering, Nagoya University |
Japanese
|
〒464-8603 Fro-cho, Chikusa-ku, NAGOYA |
|
Researches
Characterization of Carbon Fiber-Reinforced Plastic (CFRP) |
|
|
Carbon fiber-reinforced plastics (CFRPs) are used as a structural material in major airplanes, e.g., Boeing 787 and Airbus A380, because of its high specific strength and stiffness. In recent years, CFRPs have been applied to primary structures such as wings, leading to weight reduction and high fuel efficiency of airplanes. Our research group performs experiments (e.g., a strength test, a fracture toughness test, and fatigue crack growth test) to evaluate the mechanical properties of CFRP laminates. We also carry out numerical simulations using a finite element method (FEM) or a boundary element method (BEM). |
|
|
|
|
Development of carbon nanotube reinforced composites |
Nowadays, carbon nanofibers (CNFs) and carbon nanotubes (CNTs) are attracting attention because of their features. Our research group investigates the mechanical properties (e.g., elastic moduli and a tensile strength) and the physical properties (e.g., an electric conductivity and a thermal conductivity) of polymer matrix composites using CNFs or CNTs as reinforcing fillers. Through these studies, we aim to develop high-strength and high-functional composite materials and examine their use as structural materials in automobiles, airplanes, etc. In particular, we focus on the study of carbon fiber-reinforced plastic (CFRP) laminates reinforced by CNTs or CNFs. |
|
|
|
|
|
|
Material evaluation by resonant ultrasonic spectroscopy (RUS) |
|
|
Resonant ultrasonic spectroscopy (RUS) is a method for determining the elastic and viscoelastic moduli of solid materials by measuring resonance frequencies. In this laboratory, an experimental system using a piezoelectric element is used to excite vibration. Then, an inverse analysis method using a boundary element method (BEM) or a finite element method (FEM) combined with a genetic algorithm (GA) is applied. We examine the technique to evaluate the elastic and viscoelastic moduli (parameters of elasticity and viscosity) of the anisotropic materials with high accuracy. |
|
|
|
|
Evaluation of material physical property by using laser ultrasonic waves |
Much attention has been paid to the testing technique using laser ultrasonic waves to measure the physical properties of the material. In this method, the irradiated laser pulse generates an elastic ultrasonic wave inside the solid materials, and the material strength is estimated by using reflections and interferences of the wave. Our research group investigates the method for measuring the interfacial adhesion strength and fracture toughness of coating films using laser ultrasonic waves. |
|
|
|
|
|
|
Damage behavior of CFRP Laminate under High Velocity Impact |
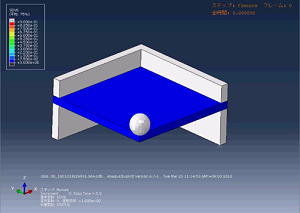 |
|
Various objects, such as birds or hails, may collide against aircraft structure during the operation. CFRP is more brittle than usual metallic materials, such high velocity impact may cause significant damage to the aircraft structure. It is, therefore, very important to predict the fracture behavior of the CFRP under high velocity impact.
In this study, we proposed a model which simulates microscopic damages, and successfully predicted damage process and extent in the CFRP under high velocity impact.
Moreover, by using knowledge derived from the simulation results, we proposed selection method for more impact resistant CFRP. |
|
|
Fracture Behavior of the CFRP Adhesive Bonded Structure under Cryogenic Temperature |
|
Coefficient of the thermal expansion (CTE) of the CFRP laminate is significantly smaller in the fiber direction, compare to those the conventional metal materials. Thanks to the small CTE, thermally-stable structure can be achieved by using CFRP. The thermally-stability is very important especially for the structure used in the harsh temperature, such as artificial satellites. Therefore, small CTE is an advantage of CFRP.
However, the small CTE may be a disadvantage under specific situations. For example, in the adhesive bonded structure consists of CFRP and metal materials, the difference of the CTE generates large thermal stress. In the cryogenic propellant tank of space launch system, failure of the structure caused by the CTE difference is a serious issue.
In this study, we investigated the failure behavior of the CFRP adhesive bonded structure under cryogenic temperature. Moreover, we proposed new structural design of the cryogenic tank based on the measured fracture behavior. |
|
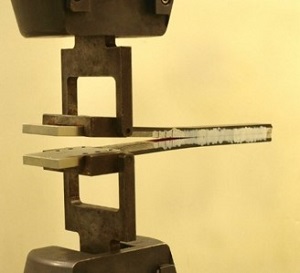 |
|
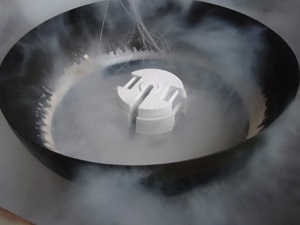 |
Visualization and Modeling of Microscopic Structure in CFRP by X-ray Computed Tomography |
|
|
|
X-ray Computed Tomography is a technique which can acquire internal tomographic images by processing many X-ray transparent images. Recent improvement of the performance of the system allows us to investigate microscopic internal defects, such as carbon fiber waviness and matrix voids.
In this study, we evaluated the internal microscopic defects in CFRP statistically.
Moreover, we develop the method which makes microscopic simulation model of CFRP, directly from the X-ray CT images. |
|
|